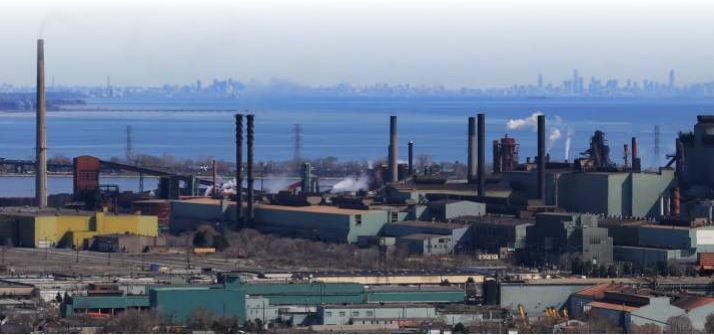
A Note on Vapi Industrial Estate
Vapi GIDC (Gujarat Industrial Development Corporation) has completed 50 years recently. Out of the entire lot of industrial units, about 30 units had started in 1968; only a few of them are still in operation. In 1968, Vapi was sleepy town with a population comprising less than 50,000. Most of the land acquired by the GIDC was grassy land. There was only one factory at that time, namely 'Aegis'. In 1968, when the GIDC developed the 1st Phase of Vapi Industrial Estate, about 30 units, mainly built by
‐ Satish Zaveri
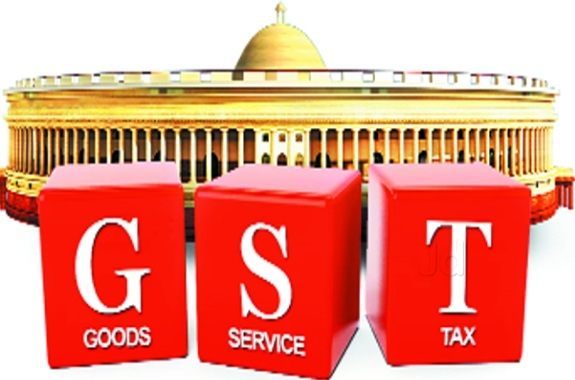
Cabinet approves proposal for Amendment to the Micro, Small and Medium Enterprises Development Act, 2006 to change the criteria of classification and to withdraw the MSMED (Amendment) Bill, 2015 – pending in Lok Sabha
Read More
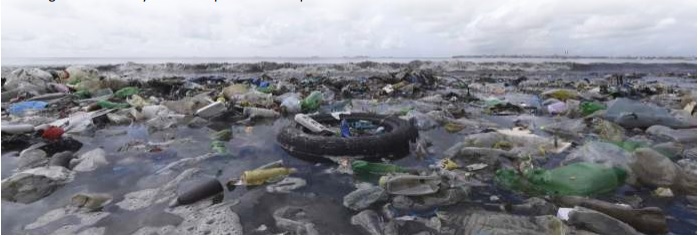
Europe tackles plastics waste
New strategy targets recycling of more than half of all plastics packaging waste
Plastics Converters, say they welcome the Commission's strategy. They pledge to launch new initiatives in a bid to recycle 50% of all plastics waste‐including packaging‐in Europe by 2040.
Plastics Europe, an industry association whose members make new plastic, says it is committed to ensuring 60% of plastic packaging is reused or recycled by 2030. In an attempt to reduce the number of plastic particles entering the aquatic environment, the Commission proposes restricting the use of particles less than 5 mm in size in products such as cosmetics and detergents. The Commission also proposes that oxo‐plastics, which break down into small fragments in the environment, should be banned. Europe's new plastics strategy comes on the heels of China's ban on imported plastic waste. Many European companies now have a growing plastics waste disposal problem as a result. The EC claims its strategy will deliver economic as well as environmental benefits. Just 5% of the value of Europe's plastics waste is recovered, meaning that between $85 billion and $128 billion is lost to the region's economy every year, says Jyrki Katainen, the Commission's vice president for jobs, growth, investment, and competitiveness. The European Commission has unveiled its first‐ever Europe‐wide plan to tackle plastics waste, including waste entering the oceans. At the heart of its plan is a goal that all plastics packaging used in the region must be recyclable by 2030. The Commission also set a target to recycle 55% of plastics packaging waste‐which makes up about two‐thirds of all plastics waste generated in the region‐by then. Currently, less than 30% of the 26 million metric tons of plastics waste collected in Europe each year is recycled. Much of the rest is incinerated, placed in landfills, or shipped outside the region. The Commission will provide $120 million to fund innovations in pl a sti c s re ‐ c yc l ing , inc luding the development of processes for making plastics recyclable and systems for removing hazardous sub‐stances and contaminants. Six European plastics recycling industry organizations, including Plastics Recyclers Europe and European
- Alex Scott
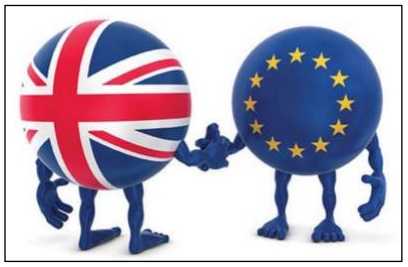
Scientific Co-operation between the UK and the EU: It's time to talk
The time has really come to maintain a co-operation between the UK and the EU for the sake of scientific pursuit of knowledge.
There are, of course, the non‐EU projects, such as those run by CERN and the European Space Agency, where involvement will carry on regardless. But, we have to accept that many see benefit in continued involvement in the 3% of the UK R&D that relies on the EU.
Nevertheless, the UK's interest in an association agreement, there seems no logical reason why our scientific relationship with the EU should change. Yes, the other EU states must agree to it, but would they exclude a nation with five of the world's top 20 universities or that has produced more Nobel laureates in science and medicine than any other EU member? As the UK takes back control of immigration, it will need to mitigate the impact on science and develop a strategy to maintain the inward flow of researchers and academics. Thankfully, there is evidence to suggest this does not require open EU borders. A 2012 study showed that states with strict controls, such as Australia, the US and Canada, recruit a greater (percentage of foreign researchers than the UK, France and Germany. It may require innovative solutions, such as a simplified fast‐track visa for researchers or the removal of genuine overseas students from immigration statistics, but the UK can continue to recruit the brightest and best minds from across the globe. With the UK's exit from the European Union (EU), it is clear that Theresa May, the UK Prime Minister (PM) wants to control the UK immigration from the EU nations by leaving the single market, thereby ending a commitment to freedom of movement. Thus raising questions over how collaboration between the British and the EU scientists on EU‐funded research will continue unhindered and how new border controls will affect the arrival of overseas scientists to the UK. There is a robust optimism that a deal can be worked out to continue joint research and that a new immigration system can keep talent arriving to the UK so as to ensure that science in the UK thrives after Brexit, a UK government priority.
Read More
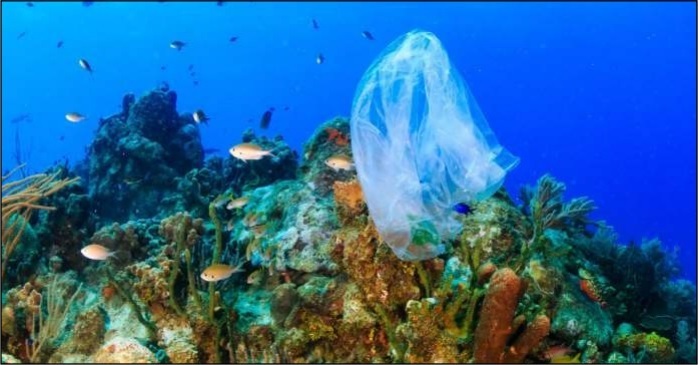
Coral reefs around the world endangered by plastic waste
Contact with plastic dramatically increases the disease for coral reefs.
Coral reefs across the globe face a threat for their very existence from overfishing, climate change, nutrient runoff and ocean acidification. Now researchers have added another hazard to the list: plastic waste. In a survey of reefs in the Asia‐Pacific region, marine biologists found that contact with plastic garbage increased corals' risk of disease from 4 to 89%, to be precise.
Researchers and environmentalists have been sounding the alarm bells about the 4.8 million to 12.7 million metric tonnes of plastic which find their way into the oceans every year. Douglas Rader, chief oceans scientist at the Environmental Defense Fund and one of the study's co‐leaders said that the strong connection between coral disease and plastic was extremely surprising. “This is striking, particularly in the context of all the other risks to reefs,” he said. The plastic waste study, an international effort involving researchers from the Cornell University and collaborators in Indonesia, Hawaii, and Australia, examined 159 reefs in Myanmar, Australia, Thailand and Indonesia. Researchers looked for signs of disease, including bands of necrotic tissue on the corals. They also noted whether the corals were in contact with pieces of plastic, 50 mm in diameter or larger. Courtney Couch, a coral disease ecologist at the Hawaii Institute of Marine Biology who surveyed reefs in Indonesia, said that she saw many corals wrapped in plastic fishing lines and plastic bags. Although the researchers didn't establish a mechanism to explain the correlation, Couch observed that plastic can carry pathogens. Plastic also can wrap around coral, which causes stress and leaves the organism vulnerable to infection. Tracy Mincer, the Marine Chemist of the Woods Hole Oceanographic Institution, who said that he read studies about plastic in the ocean with a pinch of salt, is convinced today. “It is a lot of work to do these surveys, and the increased disease susceptibility is a big signal,” he said. The study opens the door to further research on the marine‐plastic microbiome and its effects on ecosystems, Mincer added.
- Katherine Bourzac
Read More
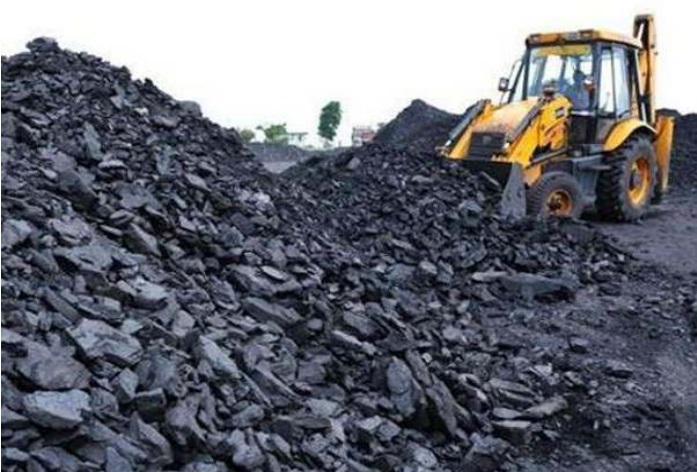
Clean Coal: The future raw material for the Chemical Industry
Doris Neukirken wrote the following in Process Worldwide in 2007: Whether coal, gas or even biomass will replace petroleum as the chemical raw material of the future is not yet clear. However, one thing is certain. Alternatives will be needed in the long term despite the fact that even pessimists predict that oil will be available for the next forty years. High prices, increasing consumption in Asia and the chaotic political situation in the oil producing countries add an element of urgency to the discussion on diversification of the raw material base. The industry is looking for an intelligent mix and an evolutionary approach to the supply of raw materials.
The chemical industry reportedly uses about 2% of the global annual oil production while so many companies are researching for alternative feedstock. Experts contend that 10 years later, in 2017, the chemical process industry is still at the crossroads. Moreover, the uncertainty has been overcome as we look to the USA with its shale gas reserves coming into play which is further clouding the future outcomes. Despite these efforts, the use of bio‐resources to make the chemicals needed by society has not yet had a significant impact. Nor has the use of municipal solid waste as a raw material. Both have been shown to be useful for the manufacture some basic solvents. What is more the technologies clearly have excellent outcomes in terms of climate change; but they are but a tiny drop in the ocean in the global petrochemical & chemical markets. Even the best of new technologies find it hard to be financially viable in the light of the fall in the price of oil (and related gas price) in recent years. The so called "valley of death" in the technology innovation pathway has for this reason become somewhat deeper. Cellulose, Lignin and Glycerine all have their proponents as industrial feedstock which can be utilized with new technologies such as ionic liquids, enzymatic transformation as well as heat intensive processing to create so called “synthetic” gases. Meanwhile more recent developments in pyrolysis techniques have enabled the conversion of MSW, Agricultural waste and Biomass to useful products. However, none of these have yet been scaled to provide industry wide alternatives products suitable for high through put bulk chemical manufacture. As an alternative and because it has large coal reserves, China has been improving new coal liquefaction and gasification technologies in order to reduce its dependence on oil. Furthermore, processes developed before the Second World War have also been used for coal liquefaction in Germany and South Africa. The Fischer‐Tropsch process converts coal to synthetic gas which can be liquefied for use as fuel or as a raw material in the chemical industry. The collection of carbon dioxide from power generation and chemical manufacture is also a potential raw material for the industry if the thermodynamics of the conversion of C02 to useful products can be overcome. Work is already underway to convert C02 chemically to carbonates and cyclic carbonates which are useful in batteries and plastic technologies. Alternatively, the use of cheap energy sources to reduce the gas with hydrogen to alkanes and indeed photo‐synthetically in artificial “leaves” is already described in the literature. These are all futuristic opportunities for supplementation of the chemical raw materials. The biggest opportunity to supply the chemical industry with the carbon it needs may in fact be the combination of these technologies ‐ gasification of coal and carbon dioxide capture, what is now being described as “Clean 00 Coal”. This requires gasification of coal deep underground to manufacture synthetic gas, then returning any carbon dioxide made during this activity (and in the processes in which the syngas is used) to the coal fields where the original gasification took place. As an alternative, any carbon dioxide produced can be put to use as raw material for products described above or sent in to other underground storage areas such as deep sea water (saline) aquifers. Most of the carbon extracted as synthetic gas in the chemical industry will be locked into products like polymers and construction materials. Clean Coal also has the potential of supplying the UK for example with all its energy as well chemical industry raw material needs. The UK lies on some very big coal reserves; remarkably the British Geological Society and Coal Board surveys have shown that in the “Durham” coalfield alone has the potential to supply the UK with all its carbon needs for over 10,000 years. A recent industrial study carried out by the North East of England Process Industry Cluster (NEPIC) has identified the medium to long term need for the UK chemical industry to find alternative raw materials.
- Dr. Stan Higgins
Read More